Share
Pin
Tweet
Send
Share
Send
Attention! Work should be carried out in a well-ventilated area, preferably equipped with active ventilation or outdoors.
To solder aluminum, we need machine oil (used to lubricate sewing machines), a small piece of sandpaper, rosin and ordinary solder for soldering radio parts.

A soldering iron is needed if possible powerful. For example, such. Its power is 65 watts.

We will solder the bottom of the aluminum beer can.
Before work, the soldering iron tip must be leveled with a file (remove all sinks) and tin.
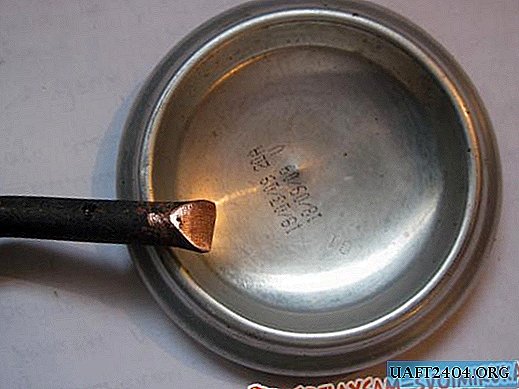

With a piece of sandpaper we clean the place of soldering to shine.

Pour some oil into this place.

Next, rub the oil stain with sandpaper.

Thus, we remove the oxide film, and the oil does not allow the formation of a new film.
The soldering iron should be warmed up to working temperature by this time.
Dip the soldering iron tip into the rosin, pick up as much solder as possible, dip it into the rosin again and start quickly with a little effort to rub the future soldering spot. At the same time, the oil begins to burn out profusely. Therefore, we do not regret rosin. If everything was done correctly, then our tin layer should cover the surface of aluminum.

Sometimes, to achieve the desired result, you will need to repeat this operation several times.

The copper wire is soldered to tinned aluminum very easily.

Now try to tin and solder the aluminum wire. Remove insulation from it and clean it to a shine. Pour machine oil onto the tinned bottom of the can.

Next, the wire must be dipped in oil and rubbed with sandpaper.

Then we try to tear the wire right at the bottom of the can. If it turned out, then everything was done correctly. If not, work with sandpaper again.

The wire is also perfectly soldered to an aluminum can.


Instead of machine oil, you can use gun. If the aluminum part is large, you may need to warm it up additionally. For example, on an electric stove.
Share
Pin
Tweet
Send
Share
Send